Common Troubleshooting of Twin Screw Extruder machine
Common Troubleshooting of Twin Screw Extruder machine
The twin-screw feed extruder is mainly composed of a barrel and a rotating extrusion twin screw in the barrel. When the equipment is running, the material enters the material chamber through the feeding port, and the screw rotates and extrudes forward to transport it. Under the action of thrust, friction, shear force and heat, a high pressure and high temperature difference is formed inside and outside the chamber. The moment the material is extruded, it expands instantly due to the pressure difference.
No material discharge due to blockage:
(1) The particle size of the raw material is too large relative to the die hole size.
(2) Too much material is fed in a short period of time and the speed is too fast.
(3) Foreign matter blocks the discharge port.
(4) The diameter of the pressure ring is too small, the water supply and steam pressure are too small, and the temperature adjustment
is insufficient.
Solution: For materials with too large particle size, crush them to the appropriate particle size; adjust the feeding speed and feeding
amount, stop the machine to check and clean foreign matter; replace the mold and readjust the water flow to ensure sufficient water
pressure and steam pressure.
Poor material forming:
Different particle diameters and shapes
(1) Uneven die hole sizes;
(2) Blade wear, cutting speed is too fast or too slow;
(3) Processing temperature is too high or too low;
(4) Improper raw material formula, material moisture content is too high or too low.
Solution: Configure appropriate die holes, check blade wear and replace in time, adjust cutting speed, modulator temperature and steam inlet.
Company :
Address :
Phone :
Email :
Skype :
Whatapp/Wechat:
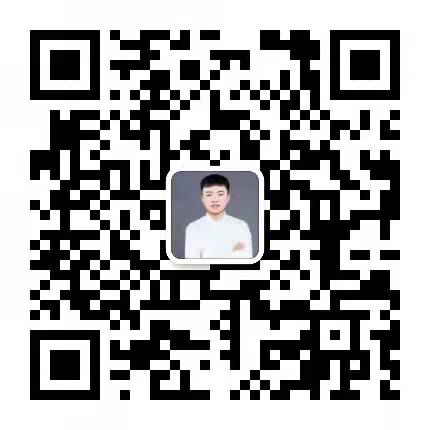