Particle crushing quality
Particle crushing quality
As we have mentioned before, there are four main factors that affect the production capacity of crushing machines: raw material characteristics, supporting auxiliary equipment, problems with the crusher itself, and the configuration of the crusher's crushing hole.
01 Characteristics of raw materials
1. Feed factories generally mainly crush various recycled materials and crop raw materials, such as straw, cotton stalks, corn stalks, corn, soybean meal, wheat, etc. And for materials that are generally difficult to crush, we refer to high oil, high moisture, high fiber, and lightweight materials that are difficult to handle.
2. In reality, our requirements are to increase the surface area and adjust the particle size of the feed, improve digestion rate, better absorb nutrients, and ultimately increase the feed to meat ratio.
3. In theory, the physical properties of raw materials. Feed materials are generally composed of starch, protein, fiber, minerals, oil, and moisture. The main factors affecting physical properties are air temperature, material temperature (materials have low-temperature brittleness, and nighttime crushing is more energy-efficient), and the difficulty level of fine crushing: fiber>protein>starch>mineral. Oil and water affect the particle size of crushing: the higher the content of oil and water, the coarser the achievable crushing fineness. The commonly used effective method for handling high moisture/high oil materials is mixing and crushing; Freeze crush.
02 Equipment itself
1. Rotational speed: The suitable range of rotational speed for a hammer crusher is generally between 60 and 70 meters per second.
The rotational speed has a significant impact on the crushing effect and equipment energy consumption. Generally speaking, excessively high or low rotational speed can lead to a decrease in crushing efficiency and an increase in equipment energy consumption. In order to achieve the best crushing effect and reduce equipment energy consumption, it is necessary to optimize the speed of the hammer crusher. Generally speaking, the rotational speed of a hammer crusher is related to the hardness and humidity of the material.
In practical applications:
For materials with high hardness, the rotational speed can be appropriately increased; For materials with high humidity, the rotational speed should be appropriately reduced. In addition, the safety of the equipment should also be considered, and excessive increase in speed should not cause equipment damage or accidents. There are many factors to consider when optimizing the speed of a hammer crusher, among which the most important are the characteristics of the material and the requirements of the production process. The appropriate rotational speed should be selected based on the characteristics of the material such as hardness, humidity, block size, and composition, and the final rotational speed value should be determined in combination with the production process requirements.
2. The rotor, machine base, rotor bracket, and turntable of the equipment are also key factors. Generally, the dynamic balance control of the rotor is within 5g
The rotation of the crusher should be processed as a whole, with a processing error of ± 0.05mm, and the axis error corresponding to the threading rod should be processed as a whole with a processing error of ± 0.05mm
Company :
Address :
Phone :
Email :
Skype :
Whatapp/Wechat:
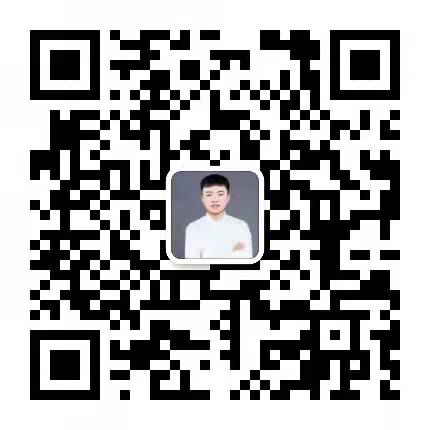